Lean-Numérique => un temps d’implémentation significativement plus court, une performance significativement plus grande
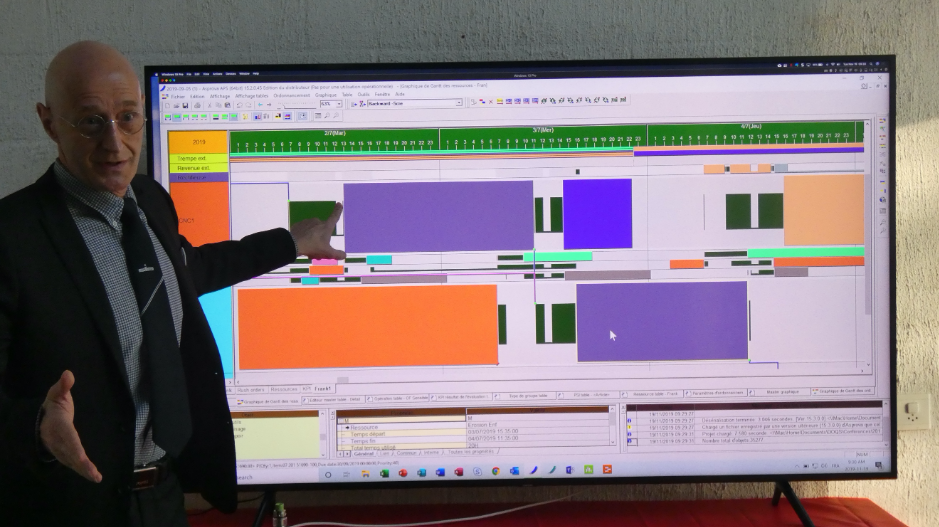
Le Lean c’est avant toute chose une culture partagée de l’excellence basée sur la promotion du collaborateur pensant. Pour étayer et guider la culture de l’excellence Taiichi Ohno a mis en place une structure spécifique d’organisation de production. Cette structure est basée sur 2 points essentiels qui sont le “juste à temps” et le “séquencement”. Une fois en régime stable, les files d’attentes sont inversement proportionnelles à la qualité ; plus les files d’attentes sont courtes et plus la qualité doit être maîtrisée sinon nous risquons d’avoir une interruption de production. Le “juste à temps” et le “séquencement” sont les fondements de la gestion de production du Lean-Numérique parce que c’est là que réside la performance. Le Lean “standard” est devenu le “Lean du XXème siècle”.
Dans le Lean du XXème siècle, cette structure se base sur beaucoup de calculs aux travers de VSMs et sur une implantation physique de Kanbans pour gérer les files d’attentes. Grâce à l’intelligence artificielle du logiciel ASPROVA, le Lean-Numérique remplace avantageusement les calculs et les Kanbans. La synchronisation se fait en quelques secondes et elle est communiquée par l’intermédiaire d’écrans dans les ateliers.
La gestion de production avec Lean-Numérique représente la réalité, elle est dynamique, réactive et libère beaucoup de temps pour la réduction de Muda-Mura-Muri => 1) l’amélioration du standard numérique 2) le Kata et 3) le 6Sigma qui tous ensemble forment la matrice du collaborateur pensant.
Une organisation Lean n’est jamais terminée car l’excellence n’a pas de fin, en revanche le Lean-Numérique permet une organisation plus performante et plus agile, elle libère beaucoup de temps pour avancer sur les éléments culturels.
La gestion de production avec le Lean-Numérique se déploie facilement
Le Lean-Numérique se déploie à l’identique du Lean classique. La partie numérique est très performante lorsqu’elle permet de synchroniser toute l’entreprise des commandes aux achats de matières premières, néanmoins elle procure également l’avantage de se déployer processus après processus afin de ne pas générer une disruption qui pourrait générer un déphasage avec le rythme de l’évolution culturelle.
Lean-Numérique pour I4.0
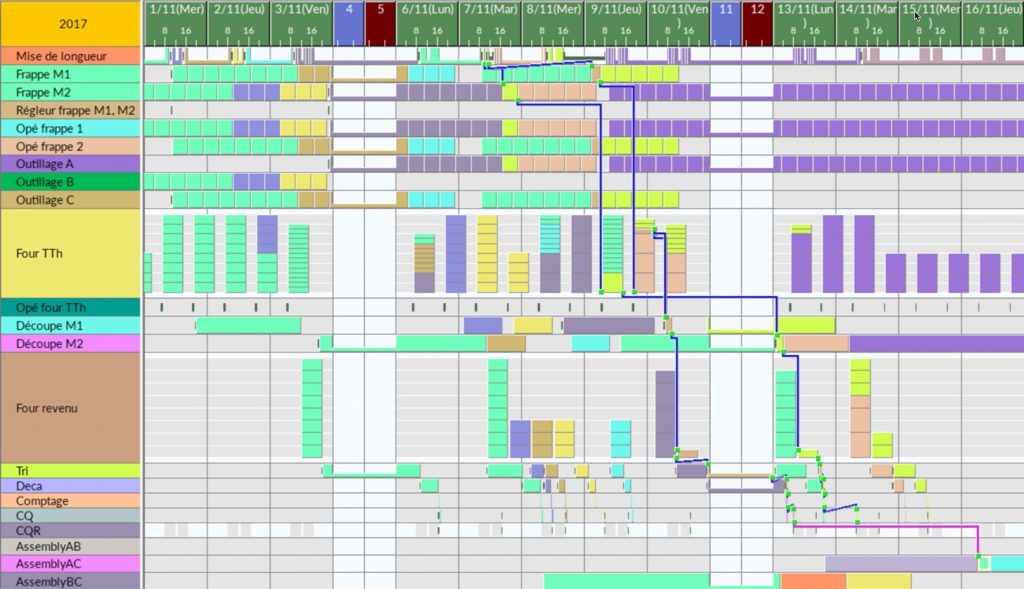
À l’heure où l’on reconnait de plus en plus que les entreprises qui ne prennent pas en considération le numérique dans l’organisation de leur production seront à court ou moyen terme vouées à la faillite, le 99% des fabricants européens, y compris des sociétés de renommée mondiale, planifient leur production avec ERP – en fait – avec Excel, papier et stylo.
Que manque-t-il?
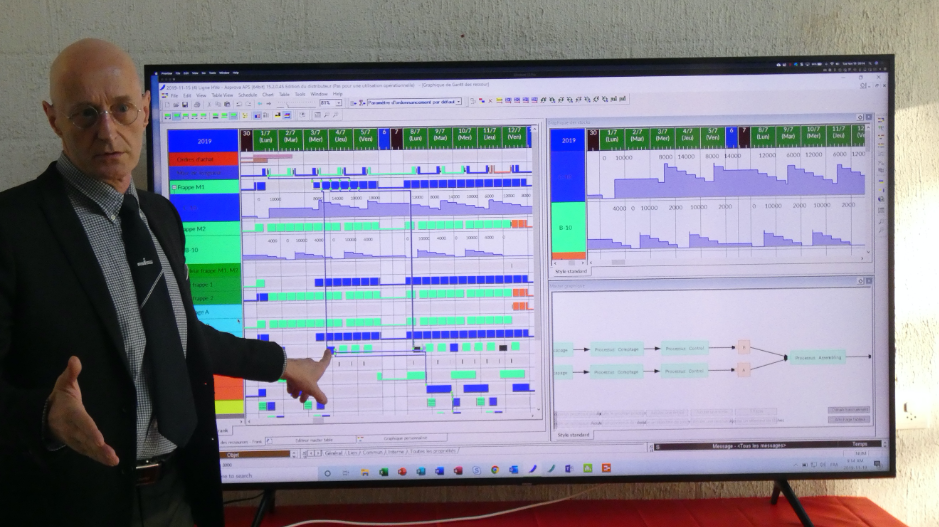
Aujourd’hui de nombreuses entreprises ont connecté leurs MES (Manufacturing Execution System) et WMS (Warehouse Management System) au système ERP et de plus en plus d’entreprises mettent en œuvre des applications IoT; Ceci n’est pas suffisant, c’est comme Google Maps où il manquerait des routes. Il faut un système de planification de la production très détaillé qui constitue le cerveau de l’usine, par lequel tous les organes de l’entreprise sont alignés pour accomplir leurs activités juste à temps. Dans le cas d’une planification de production manquante ou inadéquate comme avec ERP+MES, les gaspillages les plus chers émergent. Pourtant, le sujet de la planification de la production n’est guère mentionné dans les revues qui traitent de l’industrie 4.0.
Pourquoi ce retard ?
Cela peut être dû à un manque de sensibilisation ou simplement de l’ignorance des top managers, car beaucoup d’entre eux ne comprennent pas suffisamment leur propre réalité. Ils croient que l’ERP et le MES fournissent une méthode de planification adéquate tandis que leurs planificateurs doivent utiliser Excel, qui correspond en substance, à “éteindre les incendies”.
En effet, ERP + MES ne peut garantir la réalisation de la synchronisation des processus et la meilleure planification de séquences possible.
Gestion de production axée sur le TRS
Si les machines communiquent entre elles et sont configurées pour combler automatiquement les lacunes de capacité, on parle d’un schéma de réflexion axé sur le TRS. Dans la pratique, on entend maintes et maintes fois que les CEO et les directeurs financiers aiment présenter les commandes selon ce schéma “TRS”. Leur argumentation est la suivante : « Les machines avec des taux horaires élevés doivent fonctionner à tout moment » Ceci n’est pas correct pour une simple raison : le fait qu’une machine fonctionne ou non n’affecte pas ses coûts fixes existants. Cependant, le coût variable de l’entreprise peut être affecté, et il s’agit, pour la plupart, de coûts de matériaux – représentant souvent plus de 70% des coûts de fabrication – et ces coûts se retrouvent dans les stocks. Ainsi, le principe suivant doit être conservé :
- Produire uniquement ce qui est nécessaire
- Lorsque cela est nécessaire
- Dans la quantité exacte requise.
En d’autres termes : seules les ressources “goulot d’étranglement” doivent toujours être en route, tandis que les autres ressources ne doivent être exécutées que lorsqu’elles sont requises. C’est le secret du système de production Toyota, à savoir la production selon le temps TAKT, qui est le fondement de la synchronisation des processus et de la production “Juste à Temps”.
Le Lean-Numérique avec un excellent APS (Planification et Ordonnancement Avancé) comme prérequis à I4.0
Un logiciel de Planification et d’Ordonnancement Avancé doit être considéré comme le lien manquant entre l’ERP et le MES. Avant que les entreprises manufacturières conceptualisent l’idéal de l’industrie 4.0, il est impératif que la direction analyse et remette en question sa méthode et son système de planification de la production actuels. Les processus non synchrones, les longs délais de production et les stocks élevés sont, dans une large mesure, le résultat d’une planification de production inadéquate.
Un bon outil de planification de la production émet les ordres de fabrication vers des ressources individuelles avec des spécifications pour une séquence optimale. Une méthode de planification des séquences, coordonnées en continu est la condition préalable à la synchronisation des processus. La précision et la synchronisation correcte du séquencement sont essentielles au niveau du juste à temps.
Formation en Lean-Numérique
Pour gagner en autonomie, formez vous dès à présent!
Comment déployer le Lean-Numérique 8 jours
Lean-Numérique 6Sigma Black Belt 20 jours
Prototype Asprova 3 jours
Kata Training 5 jours
Kaizen 4 jours
Informations sur l’auteur
Nous présenterons le Lean-Numérique le 5 Février à Technopolis, Forum Fribourg